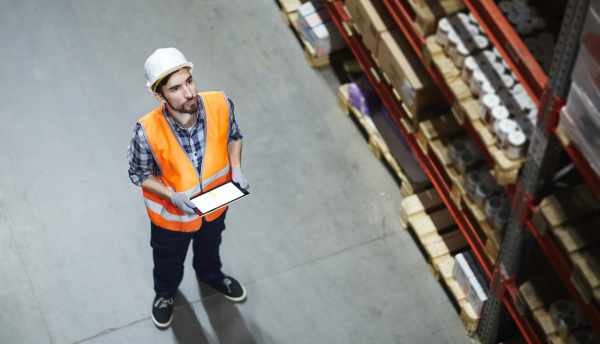
Su objetivo es evitar errores inadvertidos y corregir las ineficiencias en los procesos. Aplicando el poka yoke en tu almacén, conseguirás reducir los errores humanos en los procesos logísticos, ya que los operarios son avisados en tiempo real ante ineficiencias para solucionarlas antes de acabar su ejecución. Descubre cómo hacerlo.